Pick, pack and despatch software
Managing high product proliferation picking and despatch
At SI (Systems Integration), we’ve worked hard to find ways to overcome the daily challenges, faced by wholesale butchers. Our pick, pack and despatch software is a great example of why SI is now the UK’s leading provider of software to the catering butcher sector of the food manufacturing industry.
Our easy-to-use order collation application is ideal for picking within a high product proliferation environment, and ensures what’s delivered is correct and matches your sales orders.
For catering butchers that operate on a first-in-first-out stock basis, our despatch scanning solution expedites the process and eliminates manual errors.
Simply, scan the product label, key in the quantity for despatch and the software automatically allocates stock to orders.
Picking staff can scan each product or pack into the catering box itself
Always know when the collated order can be registered as 100% complete.
Automatically produce case end labels for each box, comprising customer details, addresses, and other specific details, such as brand-related information, and other key validation details.
Have access to real-time shop-floor data, to provide a customer with all the evidence needed to prove traceability.
Despatch Tracker from SI cuts credits by removing human error and ensuring what’s ordered is delivered.
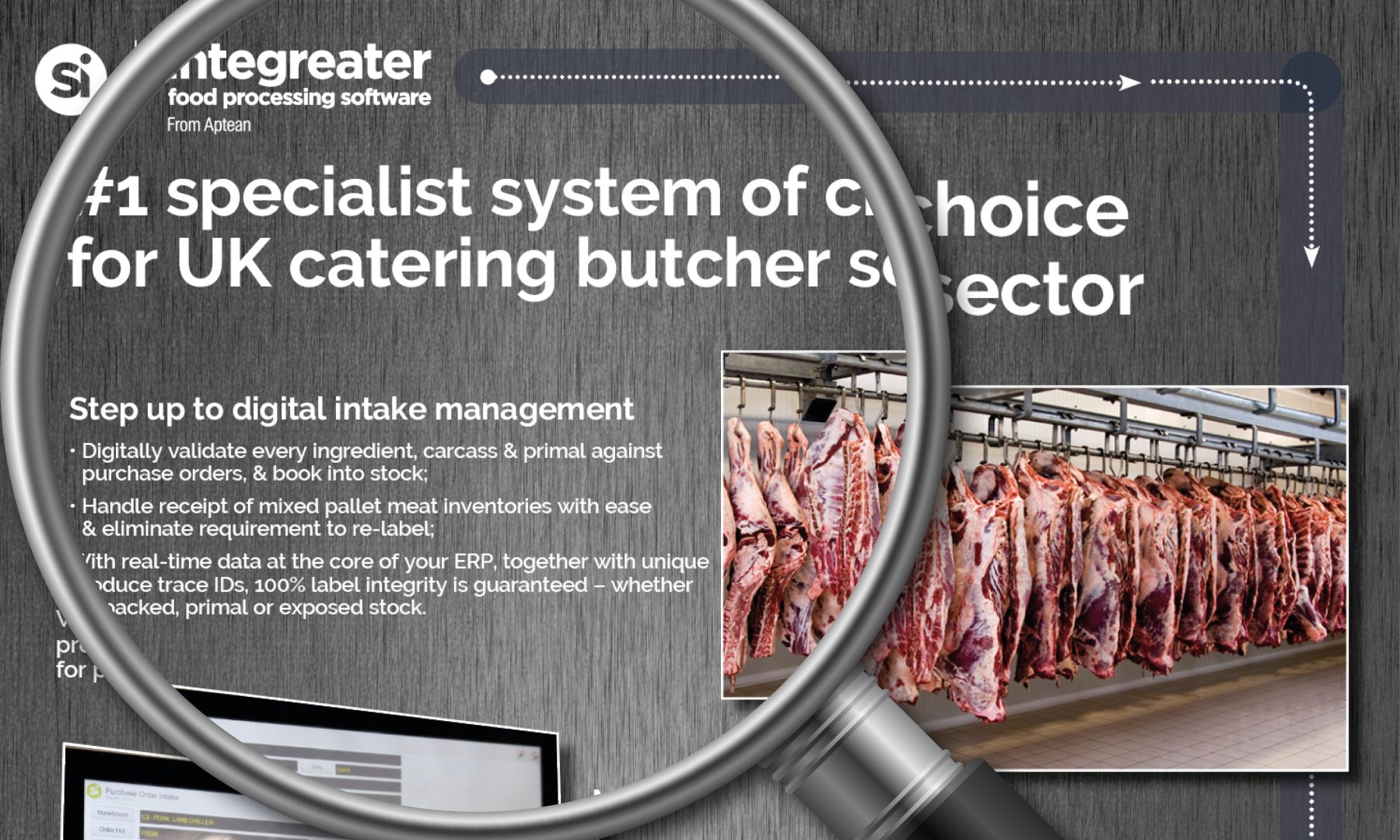